How to Manage the Warehouse Labor Shortage
Nationwide labor shortages have caused major problems in every industry. This is especially problematic in warehousing, as delays in this sector can quickly have a trickle-down effect that ultimately compromises the entire economy.
The current labor market is especially worrisome in the transportation, warehousing, and utilities sectors, where 479,000 job openings were reported as of January 2022, an increase of 25% from the previous year. Until these vacancies are addressed, e-commerce businesses will likely face reduced productivity, increased safety concerns, and ultimately lower customer satisfaction.
When determining how to manage the labor shortage, warehouse employee concerns should be top of mind. This calls for a layered approach, encompassing everything from diversity training to referral programs and even automation. Keep reading to learn why the labor shortage exists and what it will take to bridge the gap.
Why Is There a Warehouse Labor Shortage?
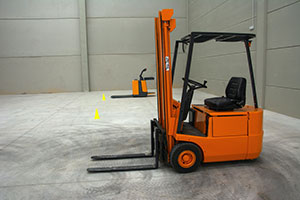
No single issue is entirely to blame for the current state of affairs. The pandemic and ensuing supply chain fiasco, however, are clear culprits, as the warehouse labor shortage escalated quickly following the initial days of lockdown.
Still, several contributing factors were evident long before COVID took over, as seen in a report from Deloitte and The Manufacturing Institute. Several of these issues are examined in detail below:
High Turnover Rates
While some employees work in warehouses for years or even decades, many remain in the positions for a mere matter of months before moving on to other jobs. The reasons for this high level of turnover vary, but many employees cite the physical exertion of manual labor as a key problem. Meanwhile, the already high rate of turnover can quickly be exacerbated when competitors poach existing employees rather than revamp their efforts to find new hires.
Retirement
Much of the warehousing workforce is currently made up of Baby Boomers. Many are ready to retire, but there often aren't enough younger workers available to take their place. This is a top concern among current managers, who cite impending retirement as one of the main obstacles underscoring their struggle to address the warehouse labor shortage.
Lack of Skilled Employees
Some jobs require specialized training that most applicants simply don't have. Meanwhile, businesses may struggle to convince entry-level employees to remain in the warehousing sector long enough to take advantage of in-house training opportunities.
Employees Leaving for Other Sectors
Some employers are unwilling to commit to extensive training programs because they fear that skilled employees will inevitably leave for jobs in other industries. This is a valid concern; due to the worries about physical strain mentioned previously, many employees are eager to find jobs that require less manual labor.
How To Manage The Labor Shortage in Your Warehouse or Distribution Center
If you've recently found it difficult to attract and retain enough employees to keep your warehouse running smoothly, you're certainly not alone. This is an industry-wide problem that will take considerable effort to fix.
By implementing the following suggestions, you can see major results in a matter of weeks while removing some of the burden from current warehouse workers. Key solutions for surviving — and even thriving — in the midst of the shortage include:
Retain Experienced Employees — And Attract New Ones
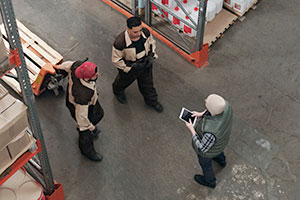
While recruitment is important, your efforts to address the labor shortage should also focus on retaining existing workers. Over time, this will prove far more cost-effective, as you won't need to spend as much time or money on training.
Let experienced employees know that their hard work is appreciated. They should never feel as if they are taken for granted by warehouse managers.
The power of higher wages and similar incentives cannot be discounted. Warehouse jobs can be challenging even under the best circumstances, so employees must be paid accordingly.
Beyond this, employees’ health, safety, and personal comfort must be emphasized. This means maintaining an orderly environment, in which automated systems and clear labeling are used to minimize unnecessary motions or other sources of strain for human workers.
Address the Physical Perils of Warehouse Work
Provide plenty of breaks and avoid scheduling employees for excessively long shifts, as this will make exhausted workers far more prone to injury. Remember: physical exertion is one of the chief factors holding full-time employees back from remaining in the warehousing industry for the long haul. Automation may be the best solution for making warehouse work safer and more comfortable.
Encourage Employees to Share Feedback
Showing respect also means making an active effort to learn about employees' workplace concerns. Give them plenty of opportunities to provide feedback without fear of retribution. From there, be upfront about addressing these issues whenever possible. After all, problems identified by your employees could have a negative impact on both retention and recruitment efforts.
Provide a Path to Advancement
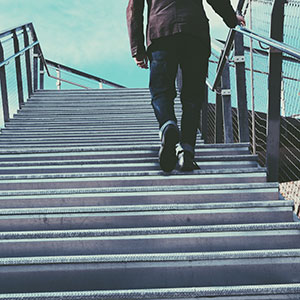
The best employees are more likely to stick around if they observe opportunities for advancement. This means not only developing a strong pipeline, but also, communicating how it functions so employees don't feel trapped. This may encompass targeted training, mentorship programs, or meetings with supervisors to discuss future plans.
Focus on Diversity, Equity, and Inclusion
How welcome do workers from different walks of life feel within the warehouse environment you've cultivated? Is it possible that some types of employees feel alienated? Diversity, equity, and inclusion (DEI) initiatives can help you expand the labor pool while helping all employees feel appreciated.
In the aforementioned survey from Deloitte, the majority of surveyed manufacturers claimed that DEI's business benefits have included "an enhanced ability to attract, retain, and develop talent." Despite this, many minority and female professionals still believe that more needs to be done in the manufacturing sector to create a diverse, equitable, and inclusive environment for all.
Consider Changing How You Hire Warehouse Employees
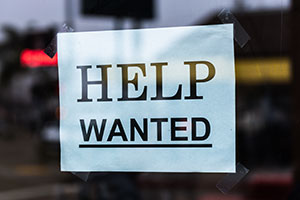
Even if your retention strategies prove effective, it's still important to cultivate fresh talent and ideas via recruitment. Rethink your outreach methods; are you attracting attention from the very best candidates? Revamp job ads placed online to ensure they fully reflect your business culture and the exciting long-term opportunities you provide. Make full use of LinkedIn and other professional platforms, as warehouse workers increasingly use these as job-searching tools.
Sometimes, the best talent comes through word of mouth. Employees love working with friends and acquaintances but may never stop to consider the possibility of referring other workers. Let employees know that their suggestions are valued; implement a referral program that actively rewards them for bringing in new talent.
Learn more about how to hire and train the best staff for your warehouse.
Automate or Improve Warehouse Systems
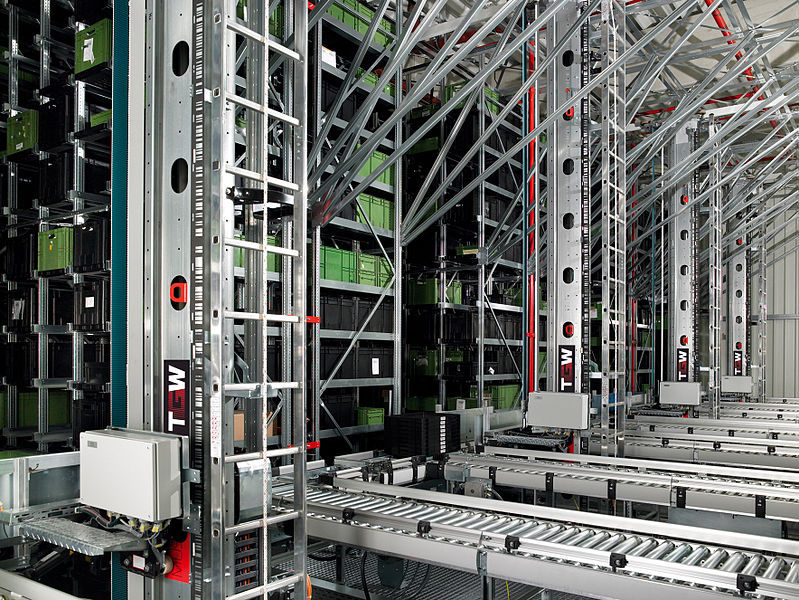
Automation can be a great strategy for improving not only efficiency but also general warehouse safety. Under this approach, the most dangerous tasks can be handled exclusively by technology.
Automation should not be regarded as a substitute for human talent, but rather, as a valuable supplement. Optimization efforts will look a bit different from one facility to the next, but the following are worth considering as you begin to explore this exciting opportunity:
- Automated storage and retrieval systems (ASRS). Meant to maximize limited floor space while also boosting productivity, ASRS makes it possible to automatically place and retrieve loads with help from strategic software and robots.
- Automated pallet shuttle systems. Featuring compact racks and electric shuttles, these pallet systems limit the need for dangerous maneuvers with forklifts and human operators. Today's automated pallet shuttle systems achieve impressive speeds. This, combined with space-saving setups, can enable high throughput in modestly-sized warehouses.
- Pallet racking systems. Pallet racking has long been a critical component of the warehouse environment, but the process can now be computer-controlled to enhance productivity. Choose pallet racking layouts carefully to boost both efficiency and storage volume.
- Motor-driven roller conveyor systems. Mounted within conveyor frames, these powerful systems are sometimes referred to as live roller conveyors. They can be used to swiftly move a variety of products and materials.
Tackle Today's Top Warehousing Challenges With Warehouse1
The modern warehousing environment may present a myriad of new challenges, but businesses that rise to the occasion will be set up for success both now and far into the future. Warehouse automation, in particular, promises to help you tackle not only the current labor shortage, but also, the evolving demands of tomorrow's tech-oriented warehouses.
Get an edge on the competition with help from Warehouse1. Our experts can help you determine which automation systems are best suited to your unique warehousing needs. Reach out today to learn more.